一、模具管理为何成为制造业的“阿喀琉斯之踵”?
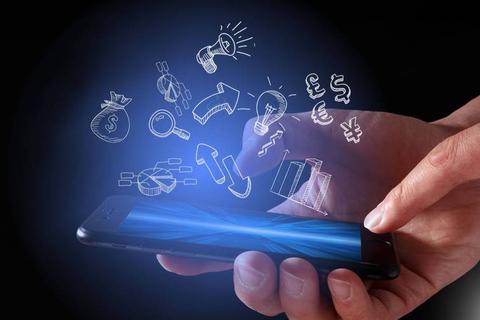
在工业4.0时代,一家年产值超10亿元的汽车零件制造商因模具管理混乱,导致价值300万元的模具意外报废,生产线被迫停工一周——这并非虚构的灾难场景,而是2018年某上市公司的真实案例。随着智能制造浪潮席卷全球,“高效能智能型模具管理软件驱动智造新纪元”已从口号变为生存法则。但矛盾在于:当模具复杂度以每年15%的速度递增时,仍有68%的中小企业沿用Excel表格管理模具。这种传统与现代的碰撞,暴露出制造业转型中的深层阵痛:如何让“工业之母”真正孕育出智能制造的果实?
二、数据中台:模具管理如何突破效率瓶颈?
广东某家电龙头企业曾因模具定位失误,每月浪费200小时人工搜寻时间。引入高效能智能型模具管理系统后,通过RFID技术实现模具定位精度达99.7%,库存周转率提升40%。这印证了现代模具管理的核心变革——从“人找模”到“模管人”的转变。
典型案例中,某外资模具厂应用智能管理系统后,成功将模具准备时间从4小时压缩至30分钟。其秘诀在于构建了包含12类模具数据的中台系统:
1. 全生命周期追溯:从采购钢材到报废回炉,每个模具的“基因图谱”完整可查
2. 智能预警机制:系统提前14天预警模具寿命临界点,维修响应速度提升3倍
3. 动态调度算法:结合车间实时负荷,自动优化模具使用序列,设备利用率突破85%
三、成本黑洞:智能系统如何重构价值链条?
苏州工业园区调研显示,未采用智能管理系统的模具企业,隐性成本占比高达22%。这些“看不见的浪费”包括:模具异常损耗(38%)、过量库存(29%)、维护延迟(33%)。而高效能智能型模具管理软件驱动智造新纪元的关键突破,正是打通了成本控制的“任督二脉”。
重庆某压铸企业的转型颇具代表性:
精准核算体系:通过工序级成本归集,单套模具维护成本降低17%
智能采购网络:对接200家供应商数据库,备件采购周期缩短60%
能效优化模型:分析1.2万条加工数据,能耗成本下降24%
该企业年度报告显示,系统上线18个月后,模具综合成本占比从19.3%降至14.6%,直接拉动净利润增长5.2个百分点。
四、生态革命:智能制造需要怎样的管理范式?
当东莞某5G基站零件制造商将模具管理系统与MES、ERP深度集成,意外收获了“1+1>3”的生态效应:模具设计迭代速度提升50%,新产品上市周期压缩38%。这揭示出高效能智能型模具管理软件驱动智造新纪元的终极形态——不再局限于工具属性,而是成为智能制造生态的“神经中枢”。
前瞻性实践包括:
数字孪生应用:某航天部件厂商构建模具全三维模型,试模次数减少70%
AI决策引擎:浙江某注塑企业通过机器学习预测模具故障,停机损失降低90%
区块链溯源:汽车供应链实现模具使用记录不可篡改,质量纠纷处理效率提升5倍
破局之路:制造企业如何跨入智能管理门槛?
对于寻求转型的企业,建议分三步走:
1. 诊断先行:利用模具健康指数评估工具(如EMOLD系统),量化现存问题
2. 模块化部署:优先实施库存定位、寿命预测等见效快的功能模块
3. 生态嫁接:选择支持API接口的系统,逐步对接现有ERP、PLM系统
据工信部《2025智能模具白皮书》预测,全面应用智能管理系统的企业,模具综合效益将提升30%-45%。在这场智能制造革命中,高效能智能型模具管理软件不仅是工具升级,更是制造业价值重构的战略支点。当最后一台模具贴上电子标签,或许就是中国制造真正迈入智造新纪元的里程碑时刻。