1. 传统工艺为何遭遇瓶颈?
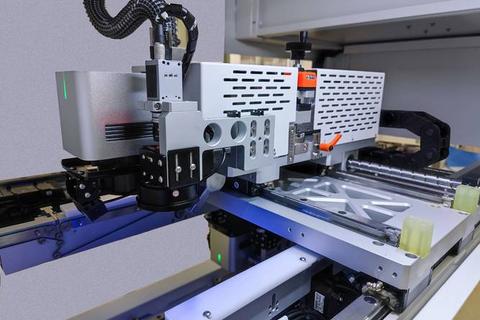
在金属加工车间里,操作员老张正对着控制台叹气:"这台进口激光机每小时成本380元,可打标误差率还是超过5%......"这样的场景折射出工业标记领域的核心矛盾:设备投入与产出效率的严重失衡。据《2023中国智能制造发展白皮书》显示,国内83%的制造企业在打标环节存在精度不足、良品率波动大等痛点,每年因此造成的经济损失高达27亿元。
正当行业陷入"高投入低回报"的困局时,金橙子打标软件智能创新轻松打造专业级工业标记效果的解决方案开始引发关注。某汽车零部件供应商的实践数据颇具说服力——在使用该软件后,其发动机缸体二维码标记的一次合格率从92.3%跃升至99.6%,单件加工时间缩短了41%。这不禁让人思考:软件革新是否真能突破传统工艺的桎梏?
2. 智能算法如何突破局限?
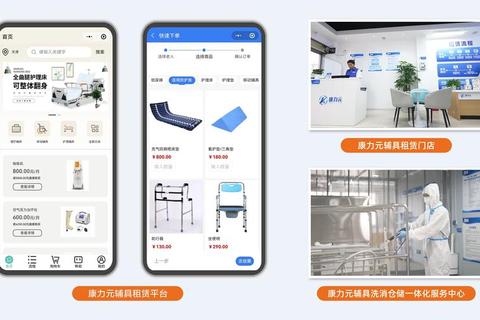
苏州某医疗器械企业的案例极具代表性。他们需要在不锈钢手术器械表面雕刻0.3mm大小的UDI码,传统软件在高速运动时常出现字符变形。金橙子研发团队通过动态路径优化算法,在2.8米/秒的加工速度下,依然保持字符边缘锐利度≤3μm。该企业质量总监透露:"自从改用金橙子打标软件智能创新轻松打造专业级工业标记效果,我们的医疗器械出口退货率从0.7%降至0.08%。
这种突破源于三大技术创新:首先是基于深度学习的材料适应性系统,能自动识别300+种材料特性;其次是实时振动补偿技术,可将设备共振造成的轨迹偏差控制在±0.01mm内;最后是智能能量控制系统,根据材料厚度动态调节激光功率,使加工深度波动范围缩小到±5μm。
3. 企业如何实现降本增效?
广东某家电龙头企业算过一笔经济账:过去在空调外壳上打标需配备3名技术员轮班调试参数,使用金橙子解决方案后,系统可根据不同批次的ABS材料自动匹配最佳参数,人力成本直降68%。更关键的是,其自主研发的批量处理引擎支持2000+个标记任务连续作业,较传统软件提速3倍以上。
在重庆某摩托车配件集群地,7家企业联合进行的压力测试显示:在连续工作120小时后,金橙子打标软件智能创新轻松打造专业级工业标记效果仍保持99.98%的系统稳定性。某轮毂制造商负责人感慨:"软件自带的智能维护模块,每年帮我们减少设备停机时间约600小时,相当于多创造240万元产值。
【可操作建议】
对于考虑技术升级的企业,建议分三步走:首先评估现有设备的通信兼容性,重点考察软件与不同品牌激光器的适配能力;其次进行小批量试加工,对比不同材料的标记效果与能耗数据;最后建立动态参数库,将成功案例的工艺参数导入企业知识管理系统。值得注意的是,金橙子提供的云端协同功能,可实现跨厂区的工艺参数共享,这对集团型企业尤其具有实用价值。
当智能制造浪潮席卷全球,工业标记领域的革新已不再是简单的设备竞赛。金橙子打标软件通过将人工智能、大数据与精密控制技术深度融合,正在重新定义"专业级"工业标记的标准。正如某行业专家所说:"未来的工业标记,比拼的不再是激光器的功率大小,而是软件系统的智慧程度。"这种转变,或许正是破解传统制造困局的关键钥匙。