当传统散热设计遭遇瓶颈,如何破局?
电子设备的功率密度逐年攀升,而散热设计却面临“既要性能,又要成本”的双重挑战。传统经验公式和试错法耗时费力,甚至可能因参数组合爆炸而陷入僵局。例如,某通信设备厂商在设计5G基站散热器时,尝试了上百种基板厚度和肋片间距组合,最终仅凭经验选择了次优方案,导致散热效率低于预期15%。这种困境并非个例——如何在复杂参数中快速找到最优解?如何平衡仿真精度与效率?这些问题催生了新一代智能散热优化工具的需求。
一、参数组合千变万化,如何实现“一键优化”?
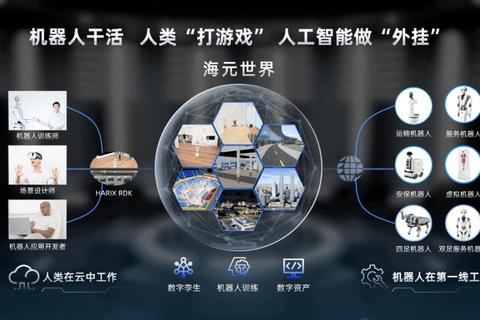
Flotherm的Command Center模块给出了答案。该模块通过集成实验设计(DoE)、响应面法(RSO)和序列优化(SO)算法,将传统人工迭代转化为自动化流程。以某服务器厂商的CPU散热器设计为例:工程师将基板厚度(2-10mm)、肋片高度(5-20mm)、间距(3-8mm)等8个变量输入系统,Command Center在72小时内完成1200组仿真,自动筛选出散热性能提升22%、材料成本降低18%的最优方案。这种“仿真机器人”模式,将多目标优化效率提升10倍以上。
更值得关注的是其全局敏感性分析功能。例如在新能源汽车电控模块设计中,Flotherm通过蒙特卡洛模拟发现:散热器基板厚度对温升的影响权重仅为7%,而肋片间距的贡献度高达63%。这一洞见直接指导厂商调整研发资源,将原本用于基板工艺升级的300万元预算转向肋片精密加工设备采购。
二、模型精度与计算速度,如何鱼与熊掌兼得?
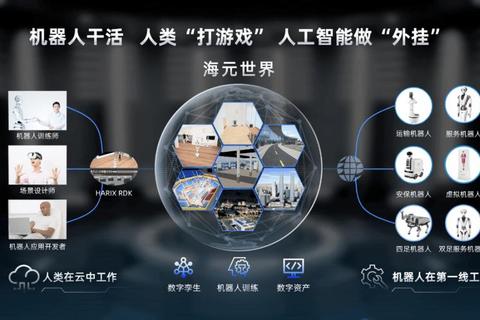
Flotherm的智能建模技术打破了这一矛盾。其专利的Cut Cell网格技术,可在保持复杂几何精度的将网格数量减少70%。某航天设备厂商在卫星通信模块散热仿真中,传统方法需生成1200万网格,耗时8小时;而Flotherm通过嵌入式局部加密,仅用280万网格即达成同等精度,计算时间缩短至1.5小时。
SmartParts参数化库更是革命性突破。以IGBT模块散热设计为例:工程师调用预置的“热管-翅片”组合模型,仅修改3个参数(热管直径、翅片倾角、接触面积),10分钟即完成原本需要2天的手动建模。更关键的是,这些模型经过2000+企业案例验证,误差率控制在3%以内。对于异形结构,Voxelization体素化技术可将CAD模型自动转化为热仿真专用格式,相比传统STL转换,几何保真度提升40%。
三、从单点突破到系统协同,如何打通散热全链条?
Flotherm的生态系统整合能力,正在重构散热设计流程。通过EDA Bridge接口,可直接导入Cadence Allegro的PCB布线数据,精确计算铜层焦耳热。某光伏逆变器厂商利用此功能,发现某MOSFET下方3mm²区域的电流密度超标,导致局部温升比预期高17℃,从而及时调整布线方案。
在实验验证环节,T3STER硬件与仿真模型的闭环校准技术,将模型置信度提升至98%。某汽车电子厂商对车载芯片进行热测试时,实测结温与仿真结果偏差达9℃;通过自动参数反演,系统识别出封装材料导热系数录入错误,修正后偏差缩小至0.8℃。这种数物融合的“数字孪生”模式,正在成为行业新标杆。
迈向智能散热设计的行动指南
1. 早期介入原则:在概念设计阶段即导入Flotherm,可利用其参数化模板快速评估不同散热路径。某消费电子企业将散热仿真前移至ID设计阶段,使产品开发周期缩短28%。
2. 数据驱动迭代:建立企业专属的SmartParts库,积累历史项目的材料属性、边界条件等数据。某数据中心运营商通过持续优化风扇曲线模型,使PUE值年均降低0.03。
3. 跨域协同机制:组建包含结构、电子、热设计工程师的联合团队,利用Flotherm XT实现机电热一体化仿真。某医疗设备厂商通过此方法,将MRI冷却系统的噪声从45dB降至38dB,同时维持散热性能。
极致高效精准仿真——Flotherm软件智能散热优化新视界,不仅是一个工具,更代表了一种以数据为核心、以协同为纽带的新型研发范式。在这个算力与热力博弈的时代,它正成为突破物理极限的关键钥匙。