一、传统BOM管理为何成为智能制造的绊脚石?
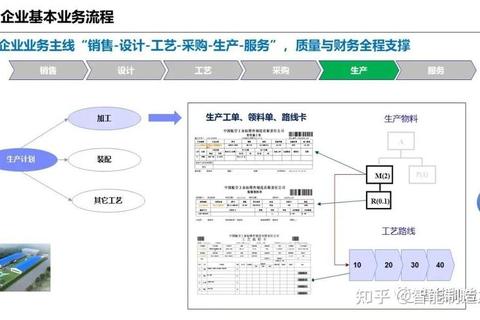
在沈阳鼓风机集团智慧数字车间建设中,工程师们发现一个惊人的现象:由于设计部门使用的BOM版本与生产系统不同步,导致价值百万的压缩机控制系统装配错误,直接造成产线停工3天,损失超千万元。这并非个例——数据显示,使用Excel等传统工具管理BOM的企业,版本混乱率高达30%,工程变更响应时间超过72小时。
BOM(物料清单)作为制造业的“数字基因”,其管理效能直接影响着40%以上的生产成本与30%的生产周期。但在智能制造浪潮下,传统管理模式暴露出三大致命缺陷:数据孤岛导致跨部门协作效率低下,手工操作引发版本失控,静态清单难以应对动态市场需求。这些问题犹如隐形锁链,束缚着企业向数字化深水区迈进。
二、智慧BOM管理系统如何破解行业难题?
当沈鼓自控引入威图与易盼的“三维设计+智能线束加工”解决方案时,车间发生了颠覆性变革:WT 36线束加工中心实现36种导线全自动处理,EPLAN Smart wiring软件将接线效率提升300%,三维部件库扩充至2000多个,最终使设计效率提升40%、沟通成本降低70%。这揭示了智慧BOM管理的三大核心突破:
1. 全链路数据贯通:通过PLM与ERP系统集成,某家电企业实现从设计到售后的BOM数据自动流转,工程变更处理时间从5天压缩至8小时。
2. 动态感知与决策:某装备制造企业应用AI预测模型,库存周转率提升25%,呆滞物料减少60%。
3. 可视化协同平台:航空航天企业采用三维可视化BOM后,装配指导效率提升300%。
这些案例印证了高效精准驱动智能制造革新:BOM管理软件智慧升级方案的核心价值——将静态清单转变为动态决策中枢。
三、BOM智慧升级能创造哪些可见效益?
金蝶云·星空PLM系统的实践数据显示,实施智能BOM管理后,某阀门企业物料齐套率从82%跃升至98%,产品上市周期缩短40%。更值得关注的是碳足迹BOM、动态BOM等创新形态的出现:
成本控制:某汽车零部件厂商通过BOM智能分析,精准定位占总成本18%的非必要组件,年节省采购费用超2000万元。
柔性生产:家电巨头利用配置化超级BOM,支持10万+产品组合的快速配置,订单响应速度提升50%。
绿色制造:嵌入碳排放数据的BOM系统,帮助工程机械企业单台产品碳足迹降低23%。
这些成效表明,高效精准驱动智能制造革新:BOM管理软件智慧升级方案已从成本控制工具进化为战略级数字化引擎。
四、企业如何踏上BOM智慧升级之路?
基于50+制造企业转型经验,建议分三步实施:
1. 基础重构:统一物料编码体系(某龙头企业借此降低90%错误率),建立模块化BOM架构(复用率提升至75%)。
2. 系统选型:选择支持微服务架构的平台(如智橙PLM),确保与MES、SCM等系统无缝对接。
3. 场景深耕:在工艺优化环节应用数字孪生BOM,在售后环节探索认知型BOM交互。
某医疗器械厂商的实践颇具借鉴意义:通过搭建变更影响分析模型,将决策时间缩短80%,同时建立覆盖3000+供应商的实时预警网络。这提示企业:BOM管理升级不仅是技术革新,更是组织流程的重塑。
当传统制造业站在数字化转型的十字路口,高效精准驱动智能制造革新:BOM管理软件智慧升级方案正成为破局关键。它不仅是连接虚拟设计与实体制造的桥梁,更是企业构建数字竞争力的核心基础设施。那些率先完成BOM智慧跃迁的企业,已在这场智能制造竞赛中抢得先机。